Hot Products
Recycling Process of MRF (Material Recovery Facility) factory
The recycling process of MRF (Material Recovery Facility) factory mainly includes the reception, pretreatment, sorting, processing and final reuse or disposal of waste. The following is a detailed process description:
1. Waste reception
• Transportation and unloading: transport the collected waste (such as municipal domestic waste, industrial waste, construction waste, etc.) to the MRF factory and unload it in the designated area.
• Weighing and recording: weigh the waste entering the MRF and record the source, type and weight of the waste.
2. Pretreatment
• Preliminary sorting: remove large pieces of non-recyclable materials such as bricks, wood, large metal components, etc. by manual or mechanical means. This step can reduce the wear and clogging risks of subsequent equipment.
• Crushing: use a shredder or crusher to break the waste into smaller sizes for subsequent sorting and processing. For example, large plastic products, metal components, etc. need to be crushed before entering the sorting stage.
• Magnetic separation: Use magnetic separators to remove ferromagnetic metals such as iron and steel from waste. This step can improve the efficiency of subsequent sorting and recover valuable metal resources.
• Wind sorting: Use wind sorting equipment to separate light combustibles (such as plastics, paper, etc.) and heavy non-combustibles (such as glass, sand, etc.).
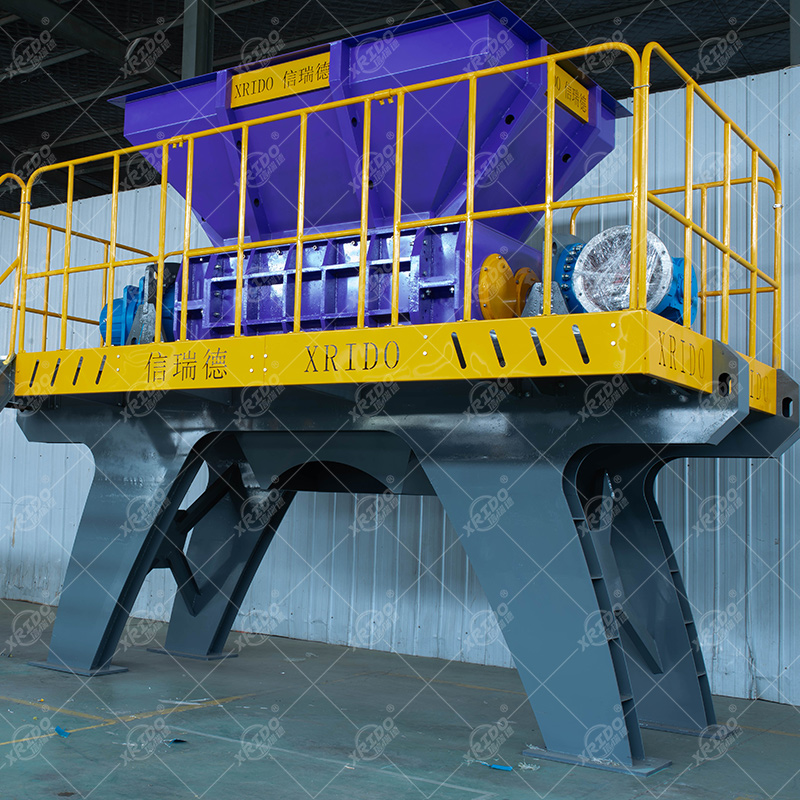
3. Sorting
• Automatic sorting: Use optical sorting equipment (such as infrared spectrometers, X-ray sorters, etc.) to accurately classify different types of plastics, paper, glass, etc. These devices can identify and separate materials based on their chemical composition or physical properties.
• Manual sorting: For some materials that are difficult to sort through automatic equipment, manual sorting is used to supplement them. Manual sorting can improve the accuracy and flexibility of sorting, but the labor intensity is relatively high.
• Screening: Use screens or vibrating screens to classify materials according to particle size and separate materials of different sizes. For example, plastic particles, glass fragments, etc. are separated by size to facilitate subsequent processing.
4. Processing
• Cleaning: Clean the sorted recyclable materials to remove dirt, impurities and residues on the surface. The cleaning process can be physical cleaning (such as high-pressure water gun washing) or chemical cleaning (such as adding detergent).
• Drying: Dry the cleaned materials to reduce the impact of moisture on subsequent processing. Drying methods include natural drying, hot air drying, etc.
• Molding or packaging: Molding or packaging the processed recyclable materials for easy transportation and storage. For example, plastic granules are made into recycled plastic products, or paper is packaged into bales and sold to paper mills.
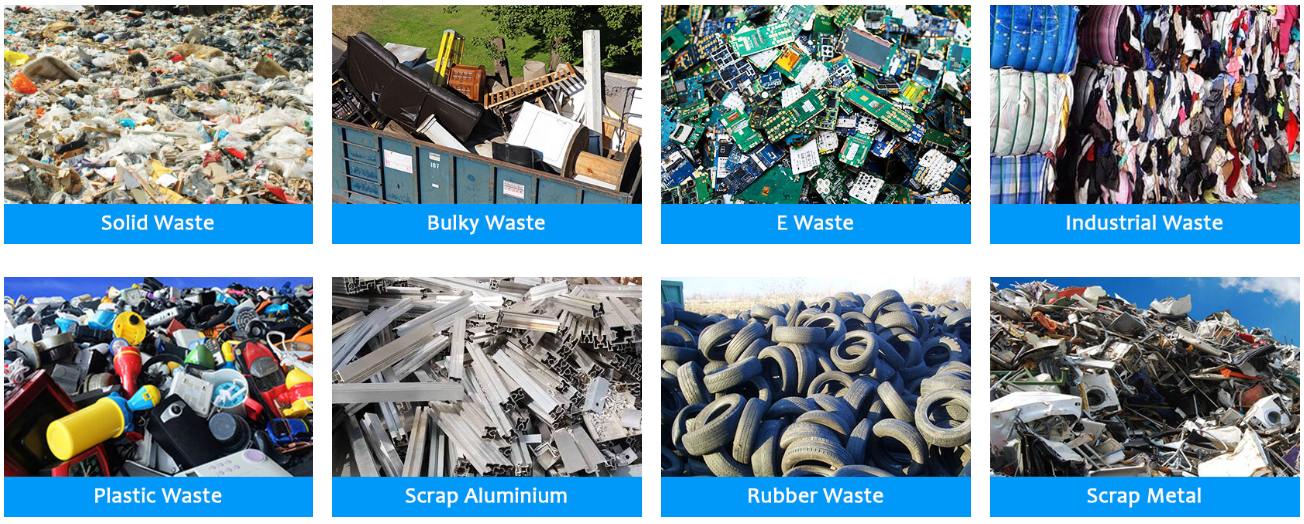
5. Reuse or disposal
• Reuse of recyclables: Sorting and processing recyclable materials (such as plastics, paper, metals, glass, etc.) are sold to related companies for the production of new products. For example, plastic granules can be used to make new plastic products, and metals can be re-smelted.
• Disposal of non-recyclables: For waste that cannot be recycled, such as residues, ashes, etc., they are usually landfilled or incinerated. In some advanced MRF plants, these wastes may be converted into energy (such as RDF fuel) for incineration and power generation.
The following is a simplified process flow for MRF plants to recycle waste:
Waste reception → pretreatment (crushing, magnetic separation, air separation, etc.) → sorting (automatic sorting, manual sorting, screening) → processing (cleaning, drying, molding/packaging) → reuse or disposal (recyclable sales, non-recyclable landfill/incineration)
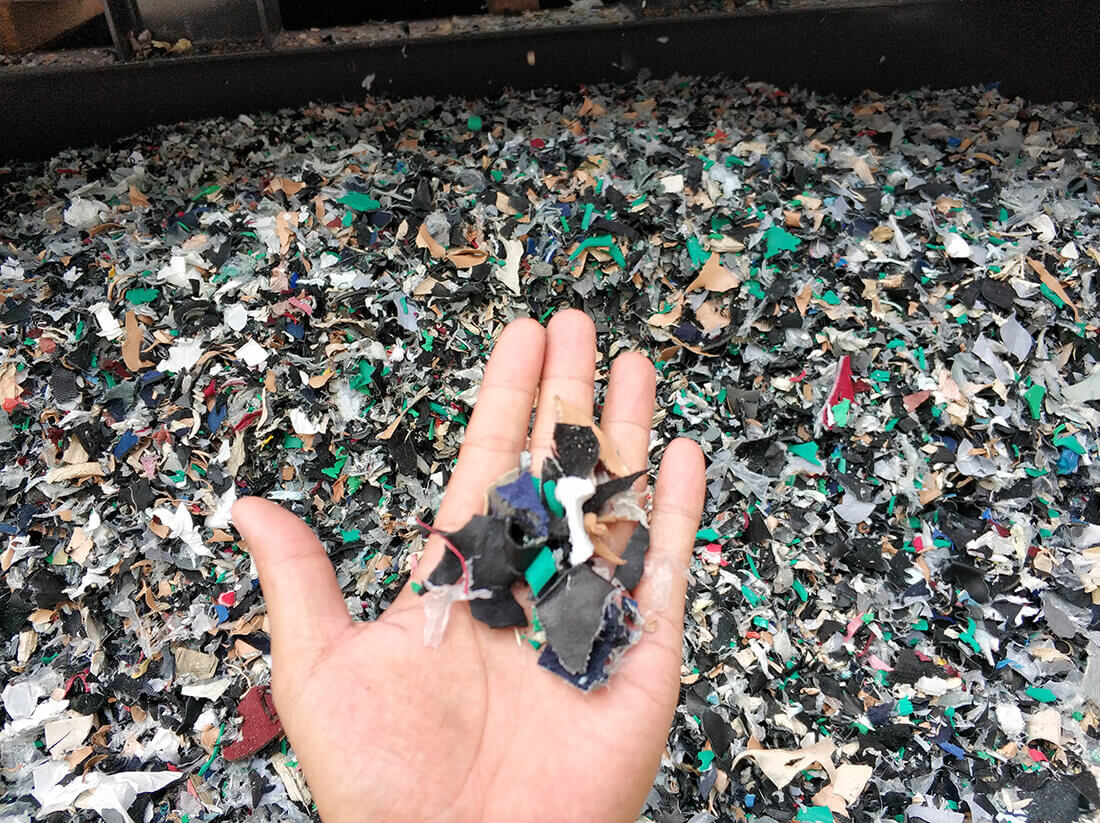
Through the above process flow, MRF plants have achieved effective waste classification, recycling and reuse, reduced landfill volume, reduced environmental pollution, and saved resources, promoting sustainable development.